小型汽轮机轴承损坏原因浅析
2013-05-13
陈贵科
(广西金光糖厂)
一般地说,汽轮机轴承在运行中如果没有外来不正常因素的影响,其寿命应该说是无限的,但是在实际使用中,往往由于供油不足,油质恶化,异物侵入,安装间隙及中心不正确,机组振动等原因导致轴承损坏。轴承损坏因素虽然是多方面的,但高速轻载汽轮机的滑动轴承损坏原因主要有两种,一是汽轮机中心偏差过大,二是轴承修刮方法不正确。
一、中心不正引起的轴承损坏
汽轮机每次检修时都要通过联轴器来正两个转子的中心,所谓找中心,就是找两个转子连接对轮的圆周,平面的错位,张口的差值,如果中心偏差过大,将会引起转子转动时的附加力,从而引起振动。此时,轴承可能受到两种情况的影响,一是由于中心不正,各轴承负荷分配不均,使某个轴承特别是联轴器两端负荷过大,超出油膜的承载能力而损坏;二是由于中心不正,通过联轴器的两根转子中心线不重合,从一个转子传递给另一个转子的圆周切线方向的力,相对于转动的中心线就不能平衡,因此引起转子及其轴承的振动,这种振动使转子不断地对轴承的合金起往复的冷作冲击作用,轴颈在上下两个半轴承间的冲击,破坏了油膜的稳定性,这种现象在受到外界因素的影响时尤为明显,如机组出力突然变化,周波变化等,如果轴承顶部间隙小,那么轴颈往复运动的范围就较小,油膜所受的冲击力自然也较小,但当轴承间隙越大时,轴顶对油膜的冲击力就越大,甚至造成激烈的振动,合金在受到往复运动轴颈的冲击下,二金属表面发生临界接触而出现自印,经长时间的冷作作用,受冲击力Z大的合金表面发生疲劳而产生微细裂缝,由于这些裂缝处于油膜压力Z高处,在振动及油膜压力的作用下,裂缝合成一个或是数个单独的密闭回路,裂缝内的合金块开始剥离、破碎。一般情况下,轴承的中间部受到的压力Z大,温度亦Z高,故损坏部位多在中间位置。轴承损坏后,由于中心发生变化,部分负荷通过联轴器转移到其他轴承,一方面减轻了该轴的受力,另一方面轴承的接触面积变大,相应地提高了承受负荷的能力,在这种情况下,除了联轴器加速磨损外,轴承受损面积一般不再继续扩大,除非中心变化太大或机组振动增大。从轴承的损坏原因,如果是中心不正引起的振动造成的损坏,一般损坏面积都比较大,运行的时间越长,损坏的面积就越大。
二、轴承修刮方法不正确引起的轴承损坏
造成轴承修刮方法不正确的主要原因有两种。一种是在轴承下部60°~120°的范围内用刮刀刮出一些花坑或井字坑,认为这样可以寸油,对润滑有利,这样做法实际上破坏了轴承的光洁度,使油膜厚度不均匀,对高转速的机组来说是不利的。一种是将轴承60°~120°的范围内修刮成与轴颈相配的触面,亦就是轴颈与轴承接触的部分与轴颈半径相等。(见图一)这种做法往往破坏了轴承与轴颈之间收缩形的契形间隙,众所周知,轴颈与油膜及旋转作用力作用下,而是稍微偏随旋转方向一定角度。此时,轴颈正好处于原来修刮好的等半径范围的边缘。(见图二)这个边缘实际上是一个凸起的部分,轴颈与轴承之间要在这个“高坡”上建立油膜是非常困难的。我们知道,轴颈与轴承之间能形成油膜的先决条件之一是必须有一个良好的契形。否则将不能承载起转子工作时的负载。由于油膜建立不良,轴颈与轴承很容易发生半液体摩擦,使轴承局部高温而损坏合金。所以,正确地修刮轴承是防止轴承损坏,提高使用寿命的重要措施之一。
总之,只要正确地掌握滑动轴承的修刮方法,合理地使用测量工具找好机组的中心,使各轴承的负荷分配符合要求,就能将轴承损坏事故减少到Z低限度,提高汽轮机的运行稳定性及安全性。
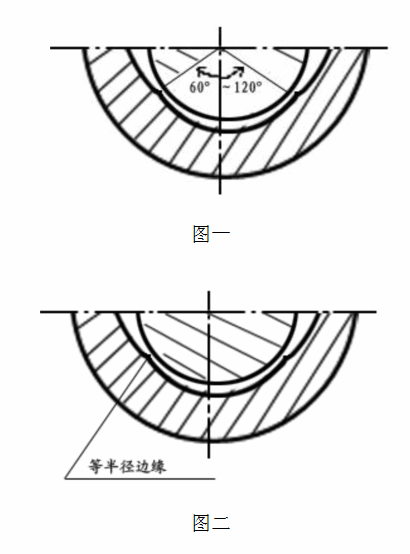